Installation and Lubrication of Universal Joints
- Preparatory work before installation
- Installation of shaft sleeves
- Installation of universal joints
- Lubrication
Preparatory work before installation
One should check models, specifications and installation sizes marked on brand labels before installation to make sure the universal joints comply with predetermined requirements.
For telescopic universal joints, factories have made phase positions of forks on both ends the same when assembling them and marked with two opposite arrow marks in the middle. Before installation, one should check the phase positions of forks again. If they are not in the right position, one should install universal joints after dismounting them and fixing forks to the right position.
Installation of shaft sleeves
Before installing shaft sleeves, one should check every part of the products to see if they comply with the design requirements. After confirmation, one can clean rags on shaft sleeves as well as the corresponding installation site.
For shaft sleeves equipped with interference joints, one should heat them through oil bath or uniform heating in induction furnace. These methods can make the axle holes swelling and more suit for installation. The heating temperature should not surpass 200℃.
Installation of universal joints
A universal shaft is composed of two universal joints and one intermediate shaft. In order to keep the driving shaft and the driven shaft go at the same angular velocity, that is ω1=ω2, the following three conditions should be satisfied.
a. The angle between the intermediate shaft and the driving shaft is equal to the angle between the intermediate shaft and the driven shaft, that is β1=β2.
b. Forks of both ends stay on the same phase.
c. The driving shaft and the driven shaft stay on the same plane with the center line of intermediate shaft.
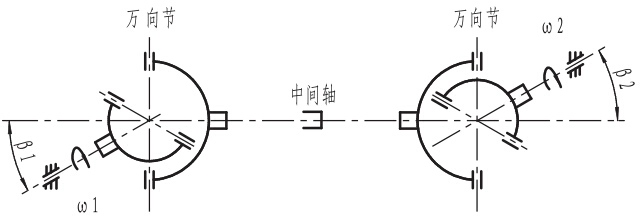
1,2-Cardon Joint; 3-Intermediate shaft
The installation types of universal joints are generally classified into Z-type and W-type, according to the relatively positions of their axis. Please refer to the following picture.
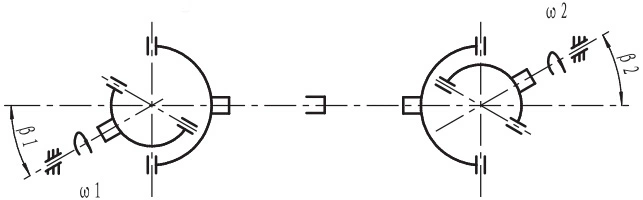
Z Shaft (Two axle parallel)
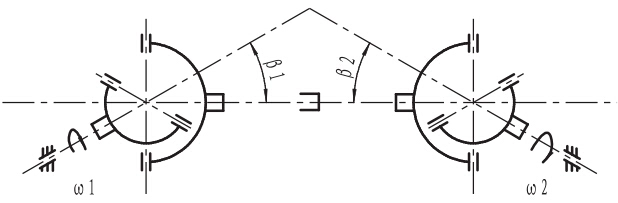
W Shaft (Two axle intersect)
When installing universal joints, one should carry products firstly to the installation position by the way designated in note 1.2. For universal joints equipped with clearance fit and flange shaft sleeves, one should fix one shaft to the shaft extension firstly and then fix the other end. For those without clearance fit, one should direct keys of driving end to the key groove and teeth to the tooth groove (castellated type and face tooth flange). Then, inserting evenly some bolts into blot holes and screwing up nuts to suitable status. Installing the driven end in the same way.
Screwing all bolts and nuts properly together with ordinary wrenches to make them completely cling to surface of flanges. Then, screwing up them with toque spanners under designated torques along crossed diagonals. Please refer to attached table 2 and table 3 for torques.
Do not hit joint bearings when installing universal joints. Do not shift universal joints with installation levers, or the sealing elements of bearings would be damaged.
Flange connection should use 10.9 grade high-strength bolts and 10 grade high-strength nuts. At the same time, use locknuts or painting tighten sealant for threads to prevent from looseness. Nevertheless, no lubricating grease is permitted.
When installing telescopic universal joints, please pay special attention in case that the spline pairs might slip off and result in accident.
In places that might cause personal and equipment accident on account of the operation of universal joints, protective cover should be set for universal joints.
Lubrication
Good lubrication is an issue of crucial importance for prolonging service life of universal joints. Therefore, lubrication should be done, especially for spline shafts, before initial operation. This can complement the parts that have not been filled before delivery. Filling lubricating grease from lubricating nozzle placed between the end of a universal joint and the middle section (telescopic type). When environment temperatures range from -20℃ to 120℃, No. 2 lithium-based grease plus 5% power lubricant is suggested. When the temperatures go surpass 120℃, it is advised to use No. 4 high temperature grease. Filling greases all the way until them overflow from the seal parts. Choosing a lubricating device as you like. In general, oil pressures are kept under 0.5Mpa. For telescopic universal joints, one should filling oil when the spline shaft retract to the extreme position for fear that the inner space might full of greases and influence the movement.
Intervals of lubrication.
After using for 500 hours, the joint bearings and spline pairs of universal joints should be lubricated once again. Since then, lubrication interval can be adjusted according to the working environment of universal joints. For those used in good environment, lubrication interval can be 6 months and others may be 3 months. For universal joints used in metallurgical and other fields, with bad, dusty, waterish or hyperthermal environment, they should be lubricated per month, or even per week.
For more information concerning universal joints, please refer to the following articles:
For more information concerning universal joints, please refer to the following articles:
Structure and Application of Universal Joints
Structural Types of Universal Joints
Model Selection of Universal Joints
Connetion Methods of Universal Joints
Carrying and Storage of Universal Joints
Usage and Maintenance of Universal Joints
Basic Info for Model Selection of Universal JointsStructural Types of Universal Joints
Model Selection of Universal Joints
Connetion Methods of Universal Joints
Carrying and Storage of Universal Joints
Usage and Maintenance of Universal Joints